Pulizia Impianto mungitura
- Klan.IT Bianchessi
- 9 apr 2014
- Tempo di lettura: 6 min
Aggiornamento: 13 set 2022
La pulizia dell’impianto di mungitura
Al termine di ciascuna mungitura è fondamentale attuare una corretta sanificazione (pulizia e disinfezione) dell’impianto di mungitura al fine di:
Ridurre la carica batterica presente nei vari componenti dell’impianto ed evitare, quindi, che essa possa contaminare il latte durante la successiva mungitura.
Ridurre il rischio di trasmissione di patogeni, agenti di mastite, tra le bovine in lattazione.
Perché la pulizia sia efficace, è necessario che l’impianto sia progettato e installato correttamente, inoltre è importante utilizzare, per il lavaggio, adeguati volumi d’acqua alla temperatura corretta e utilizzare le giuste concentrazioni per quanto riguarda i prodotti detergenti. Di fondamentale importanza è il costante monitoraggio del grado di pulizia dell’impianto per rilevare, nel più breve tempo possibile, eventuali problemi e intraprendere rapidamente le necessarie misure correttive.
Che cosa fare prima iniziare il ciclo di lavaggio dell’impianto
Prima di iniziare il ciclo di lavaggio, tutte le superfici esterne delle guaine, dei gruppi di mungitura, dei tubi e dei pulsatori devono essere sottoposti ad accurata detersione.
Purtroppo, in molti casi, questa fase preliminare del ciclo di lavaggio si riduce al solo utilizzo di un getto d’acqua, che difficilmente riesce a rimuovere tutto lo sporco esterno. Una volta che i gruppi sono stati puliti, devono essere attaccati con attenzione alle doccette di lavaggio al fine di garantire che il vuoto sia trasferito in modo adeguato al collettore, se ciò non avviene, il lavaggio di quel gruppo non avverrà in modo corretto. Eventuali sensori per la misurazione della conducibilità elettrica del latte, presenti nella linea di mungitura, dovrebbero essere controllati e puliti. Nel corso del tempo, diversi studi hanno dimostrato che il metodo migliore per detergere gruppi di mungitura e doccette è il lavaggio accurato con una soluzione detergente tiepida o calda.
Esistono diverse tipologie di sistemi di lavaggio, fondamentalmente tali impianti oggi si differenziano in sistemi di pulizia manuali e sistemi di pulizia completamente automatizzati.
Sistemi di pulizia manuali
L’operatore che si occupa del lavaggio dell’impianto di mungitura dovrebbe applicare il modo rutinario i seguenti passaggi:
1. Pre-risciacquo
In condizioni ideali, si dovrebbe introdurre nell’impianto di mungitura acqua calda a 30-40 °C. Essa rimuoverà la maggior parte del latte residuo presente nell’impianto. Al termine di questa fase l’acqua reflua dovrebbe essere eliminata.
Solitamente, per assicurare un adeguato risciacquo, sono necessari 14 litri di acqua per ogni gruppo di mungitura. Il filtro per il latte deve essere rimosso dopo questo primo risciacquo e sostituito, in seguito, con un filtro pulito. Se nella fase di risciacquo si utilizza una quantità di acqua insufficiente, residui di latte rimarranno nell’impianto. Ciò può ridurre l’efficacia del prodotto detergente/disinfettante.
2. Fase di lavaggio vero e proprio
È necessario impiegare un minimo di 14 litri di acqua calda (85 °C) per gruppo per il lavaggio principale, se non diversamente specificato dal produttore del disinfettante/detergente. In un primo momento bisogna lasciare aperto il tubo di scarico dell’acqua per consentire l’eliminazione di circa quattro litri per gruppo.
Quando l’acqua di scarico ha raggiunto una temperatura di almeno 55 °C, posizionare il tubo di mandata nella vasca di raccolta dell’acqua e dare inizio al ricircolo. A questo punto bisogna procedere con l’aggiunta del detergente/disinfettante e far circolare nell’impianto l’acqua di lavaggio, contenente il detergente/disinfettante, per 5-10 minuti. La temperatura della soluzione di lavaggio al termine di questa fase deve essere di almeno 55° C. Se il tempo di circolazione della soluzione supera i 5-10 minuti, si rischia che la temperatura scenda sotto questa temperatura soglia.
3. Risciacquo finale
Il ricircolo dovrebbe essere seguito da un risciacquo finale con acqua fredda. In genere sono necessari 14 litri di acqua per gruppo di mungitura.
Sistemi di pulizia automatizzati
Esistono molti sistemi automatizzati disponibili per pulire gli impianti di mungitura. Essi si basano sugli stessi principi descritti per i sistemi di pulizia manuali, ma funzionano in modo del tutto autonomo. Il sistema automatico, quando è impostato correttamente, può essere molto efficace. Tuttavia, questi sistemi devono essere controllati periodicamente per assicurare che si usino le corrette quantità di acqua e di sostanze chimiche e che le temperature siano adeguate. Molti sistemi presentano una variante delle routine di lavaggio standard consigliate, come un risciacquo a freddo, seguito da un secondo risciacquo a caldo, oppure due risciacqui finali. Il primo è formato da acqua pulita per rimuovere i prodotti alcalini di pulizia dall’impianto e il secondo comprende un risciacquo con acido peracetico come disinfettante.
La maggior parte delle nuove sale di mungitura sono dotate di lattodotti di acciaio inox. Il diametro delle linee del latte varia tipicamente da 70 a 105 mm. Non è possibile detergere adeguatamente tutta la superficie interna di una linea con diametro di 70 millimetri semplicemente facendo circolare una soluzione disinfettante poiché la parte superiore della linea del latte non entrerà in contatto con tale soluzione, il che può portare allo sviluppo di depositi sulle superfici superiori (Foto n. 1).
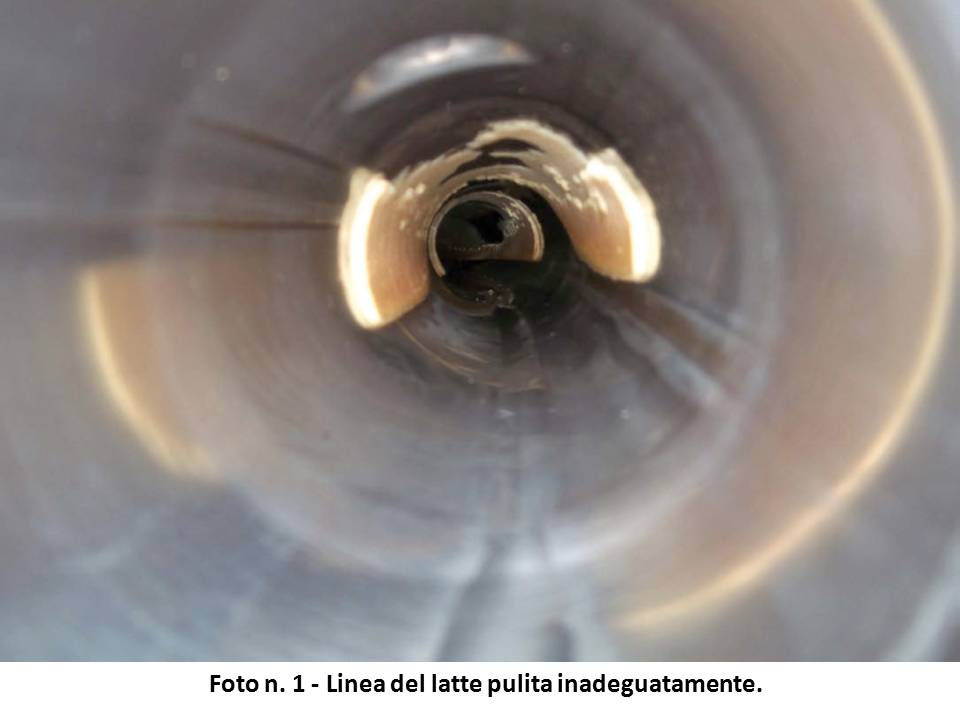
Foto n. 1 – Linea del latte pulita inadeguatamente.
Gli impianti di lavaggio delle sale di mungitura con linee del latte di diametro superiore a 50 mm si basano sulla formazione di un flusso d’acqua che lambisca tutto l’impianto e pulisca tutte le superfici interne della linea del latte. Questa condizione si crea tramite l’immissione controllata di aria nell’impianto (Figura n. 1).
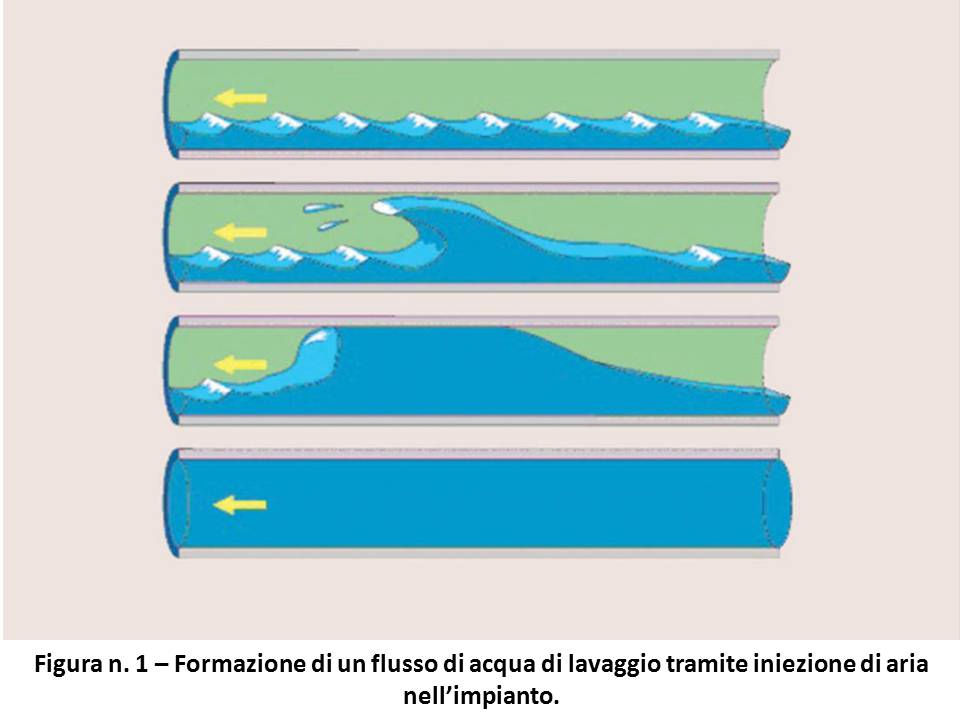
Figura n. 1 – Formazione di un flusso di acqua di lavaggio tramite iniezione di aria nell’impianto.
È fondamentale che il flusso così formato si mantenga costante per tutta la lunghezza del condotto fino all’entrata nella vasca di raccolta.
Ci sono due regole di base a questo proposito:
1. La durata dell’iniezione di aria deve essere equivalente al tempo che l’acqua di lavaggio impiega per raggiungere la vasca ricevente. Se il lattodotto ha una lunghezza di 25 m e il flusso di acqua di lavaggio si muove a 10 m/s, la durata d’iniezione dell’aria dovrebbe essere pari a 2,5 secondi.
2. Ci dovrebbero essere almeno 15 flussi di acqua per ciclo di lavaggio. Se la soluzione calda circola per sette minuti, l’intervallo tra le iniezioni d’aria dovrebbe essere pari 28 secondi.
Scelta del detergente/disinfettante
Il latte contiene grassi, proteine, zuccheri e minerali che si depositano sulle superfici interne dell’impianto di mungitura. Inoltre l’acqua utilizzata per pulire la mungitrice può contenere diversi livelli di minerali, secondo la sua durezza. I detergenti alcalini degradano i grassi e le proteine del latte e li rimuovono dalle superfici lisce dell’impianto. Tuttavia, l’ambiente alcalino che si viene a creare può favorire il deposito di complessi di proteine e calcio, calcare e altri depositi di minerali. Questi depositi possono essere rimossi solo con detergenti acidi. Tradizionalmente, i detergenti alcalini sono impiegati nella maggior parte dei cicli di pulizia con acqua calda circolante. Periodicamente, con frequenza variabile in funzione della durezza dell’acqua, al posto del detergente alcalino è utilizzato un prodotto acido in grado di rimuovere i depositi. Questi prodotti acidi concentrati (spesso a base di acido fosforico) tendono a essere molto aggressivi per i componenti di gomma presenti nell’impianto.
Per questo motivo sono comparsi sistemi di pulizia che si basano sull’uso alternato di acidi e alcali. Un uso più frequente di acido, infatti, consente la riduzione del quantitativo utilizzato a ogni lavaggio. I detergenti alcalini sono tipicamente associati a tensioattivi, agenti modulanti la durezza dell’acqua e a cloro. I tensioattivi aiutano la soluzione detergente a penetrare nelle incrostazioni, mentre gli agenti di controllo della durezza dell’acqua (fosfati e composti chelanti) mantengono minerali e sporcizia in sospensione impedendo loro di depositarsi nuovamente.
Monitoraggio della pulizia degli impianti di mungitura
La pulizia dell’impianto può essere valutata a due livelli.
1. Controllo di base
Al livello più semplice, una volta che la circolazione è stata stabilita, è importante controllare che tutti i gruppi ricevano la stessa quantità di soluzione circolante. Toccare la superficie esterna della linea del latte in siti differenti dovrebbe confermare che la soluzione raggiunge tutte le parti. È inoltre importante verificare che ci sia sempre acqua sufficiente nella vasca di raccolta per garantire che i tubi collettori siano immersi.
Se dell’aria è aspirata in questi tubi, il flusso di acqua di lavaggio è notevolmente ridotto e la temperatura diminuisce significativamente.
È anche essenziale assicurarsi del funzionamento dell’iniettore d’aria.
2. Controllo di livello superiore
È importante misurare il volume d’acqua impiegato in ogni fase del lavaggio. La temperatura dell’acqua dovrebbe essere misurata in diversi momenti: nel momento in cui lascia la caldaia, quando entra nell’impianto, prima dell’inizio della circolazione e alla sua fine. Misurare il volume delle sostanze chimiche utilizzate consentirà di monitorare la concentrazione che esse raggiungeranno nell’impianto. Il recipiente di ogni prodotto detergente dovrebbe fornire informazioni sulla sua composizione chimica e sulla corretta concentrazione alla quale utilizzarlo.
In conclusione possiamo affermare che un’efficace pulizia dell’impianto è un elemento essenziale di un sistema di produzione di latte di qualità.
Un’inadeguata pulizia dell’impianto di mungitura può causare: aumento della carica batterica presente nel latte, aumento del rischio di contagio per quanto riguarda i patogeni che causano mastiti e, conseguentemente, un aumento della conta cellulare.
I principi di pulizia sono piuttosto essenziali ma è importante che si segua una determinata routine e che tutti gli operatori preposti al funzionamento dell’impianto si assumano la responsabilità di monitorarne l’efficacia, individuando i problemi e correggendo eventuali carenze.
Fonte: Effective cleaning of the milking machine. Ian Ohnstad – UK Vet – Livestock 2013, vol. 18, n. 1, p. 28-31.
Comments